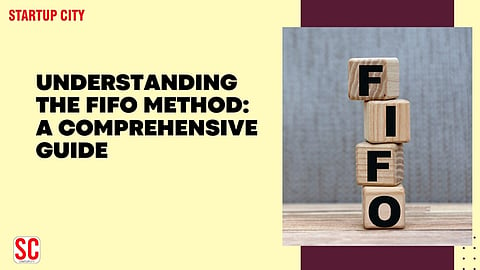
The FIFO (First In, First Out) method is a crucial inventory management and accounting technique that helps businesses manage their inventory effectively. This method assumes that the first items added to inventory are the first to be sold or used. In this article, we’ll explore the FIFO method, its benefits, applications, and its importance in various sectors.
FIFO stands for “First In, First Out.” This method is primarily used in inventory management and accounting, where it dictates that the oldest inventory items are sold or utilized before the newer items. FIFO is particularly relevant in industries where products have a shelf life, such as food and pharmaceuticals, where older products must be sold before they expire.
In practice, FIFO operates under a straightforward principle:
Inventory Acquisition: As new stock arrives, it is added to the inventory.
Sales Order Processing: When an order is placed, the inventory system identifies the oldest stock available.
Sales Fulfillment: The oldest items are picked first, ensuring that products are rotated properly, reducing waste and loss.
For example, if a grocery store has milk delivered on different days, FIFO ensures that the milk delivered first is sold first, minimizing spoilage and maintaining product quality.
In industries where products have limited shelf lives, using the FIFO method helps minimize spoilage and waste. By ensuring that older products are sold first, businesses can significantly reduce the risk of expired goods.
FIFO streamlines inventory management processes. By following a clear system where the oldest inventory is sold first, businesses can easily track inventory levels, manage stock rotation, and maintain optimal inventory health.
In accounting, FIFO affects the calculation of the cost of goods sold (COGS) and inventory valuation. When prices are rising, FIFO can result in lower COGS, which can lead to higher reported profits. This is because the older, cheaper inventory is recorded as the cost of goods sold, while the more expensive, newer inventory remains on the balance sheet.
By reducing waste and spoilage, businesses can enhance their cash flow. FIFO helps ensure that products are sold while they are still viable, allowing companies to reinvest that capital into operations or growth initiatives.
The FIFO method is widely applied across various industries:
In the food and beverage sector, FIFO is essential for managing perishable goods. Restaurants and grocery stores utilize FIFO to ensure that older inventory is sold first, preventing spoilage and maintaining product quality.
Pharmaceutical companies also rely on FIFO for managing medications and vaccines, which often have expiration dates. Proper inventory management using FIFO ensures that older products are dispensed before newer ones, reducing the risk of administering expired drugs.
In manufacturing, FIFO can be used to manage raw materials and components. By ensuring that older materials are used first, companies can avoid obsolescence and minimize waste in production processes.
Retailers benefit from FIFO by effectively managing inventory turnover. By selling older items first, they can maintain a fresh product selection and optimize customer satisfaction.
The FIFO method is a vital inventory management strategy that helps businesses maintain product quality, reduce waste, and ensure accurate financial reporting. By understanding and implementing FIFO, companies can streamline their operations, enhance cash flow, and ultimately improve profitability. As businesses continue to navigate increasingly complex supply chains, the FIFO method remains an essential tool for effective inventory management.